our Process
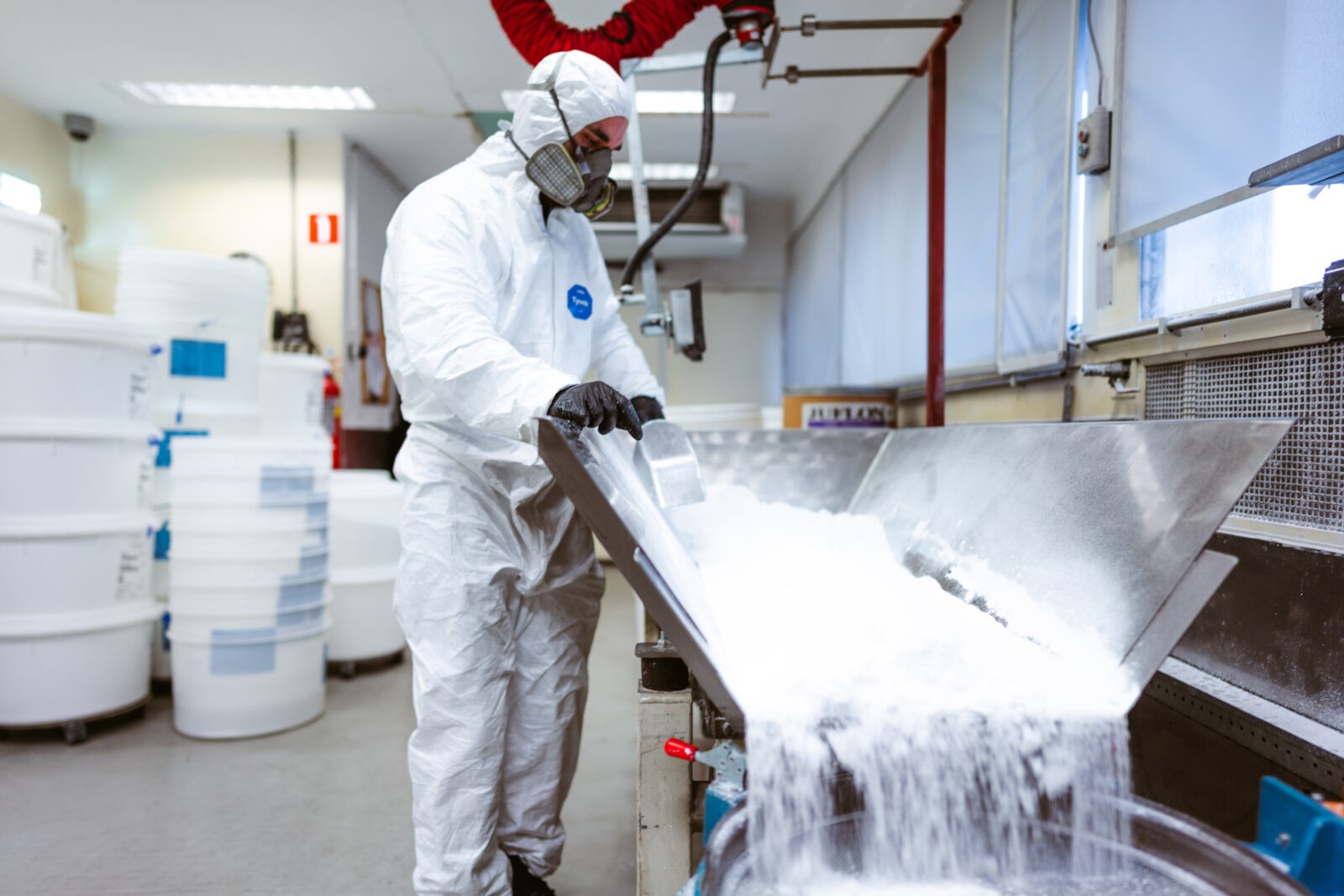
Mixing process
The mixing process is carried out in a conditioned room to avoid defects in the material
PTFE is sieved
The PTFE is sieved to prevent clumping during the mixing process.
PFTE Tubes
Fluortubing Materials
Fluortubing specializes in making thin wall tubing from PTFE Fine Powder. Over 90 % of the materials used are modified PTFE, according to ASTM D4895-91a,type I, grade 9,class B. These materials are known for their relatively low permeation rates, high flexibility and flex life, and clarity .They can be welded with PFA.
Fluortubing uses 100 % Primarily Chemours™ (Former Dupont™ ) materials, unless specified otherwise by customers. Typical grades used are : Teflon™ 62N X, Teflon™ 62XT N, Teflon™ CFP6000 X, Teflon™ 669 X. All grades used are produced without the use of PFOA. Fluortubing uses a catalytic afterburner to burn harmful vapors.
Extremely high chemical resistance
Excellent temperature resistance (-200+260)
Very low coefficient of friction
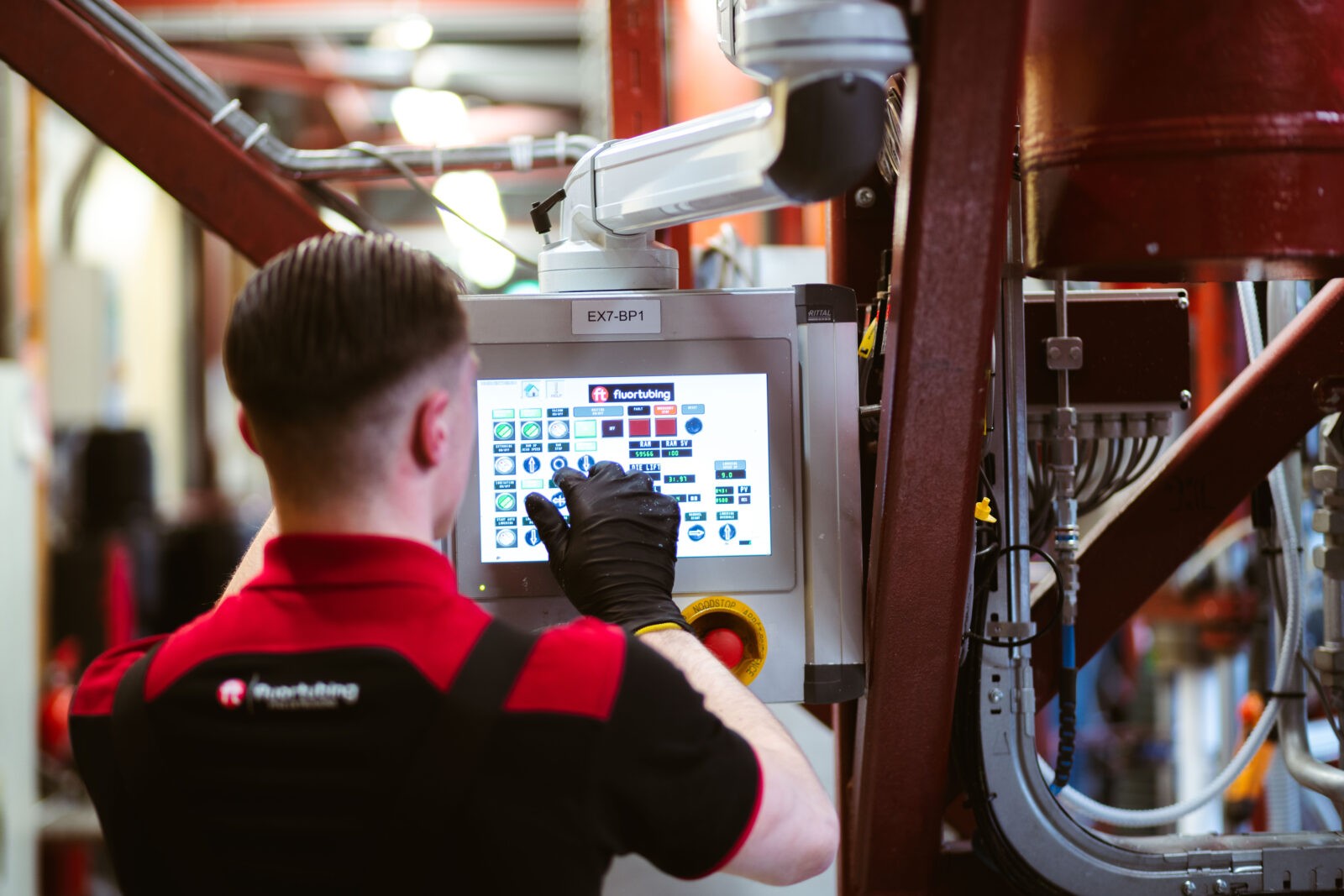
PFTE Tubes
Making the Tube
PTFE tubing or tubing of Teflon™ is extruded in a typical way that is unique for the plastics industry. The PTFE particles are coagulated in an aqueous solution to become a fine powder that is capable of absorbing a liquid lubricant. After mixing the powder with a lubricant, the material is compacted and pressed through a die and pin. The product now is in so-called green state. This product is dried and sintered in ovens.
Vapors from the lubricant are extracted. When the tubing exits the ovens, it has its strength and integrity we know. Tubing in green state is very vulnerable. That is why Fluortubing only dries and sinters in vertical ovens, that are right downstream on the extruders, thus making sure that the green tubing is untouched until it is dried and completely sintered.
Automation
Extrusion machines are automatically loaded to create stable quality.
People
Certified operators operate the extrusion lines. Operators are brought up to standard through an internal training course.
In-House Engineering
Full engineering of extrusion lines is carried out by our subsidiary Soeterbroek Engineering. This allows us to keep up with the industry in terms of automation.
PFTE Tubes
Finishing the tube
Once the PTFE Tube has been extruded and sintered, it will keep its original shape, even at melt temperature. To re-shape a PTFE tube it will usually be heated to its melt temperature and forced into the desired shape. Then it is kept in this shape until the tube has cooled to room temperature. This process enables the production of convoluted tubing, cuffs, flares, bent shapes, blow molded products and a variety of other shapes.
PTFE tubing can also be machined to size by drilling, cutting, milling and other conventional technologies. Modified types, like Primarily Chemours™ (Former Dupont™) T 62 Resins ,can be welded both by PFA wire and by pressure welding. Fluortubing offers all these technologies in one hand.
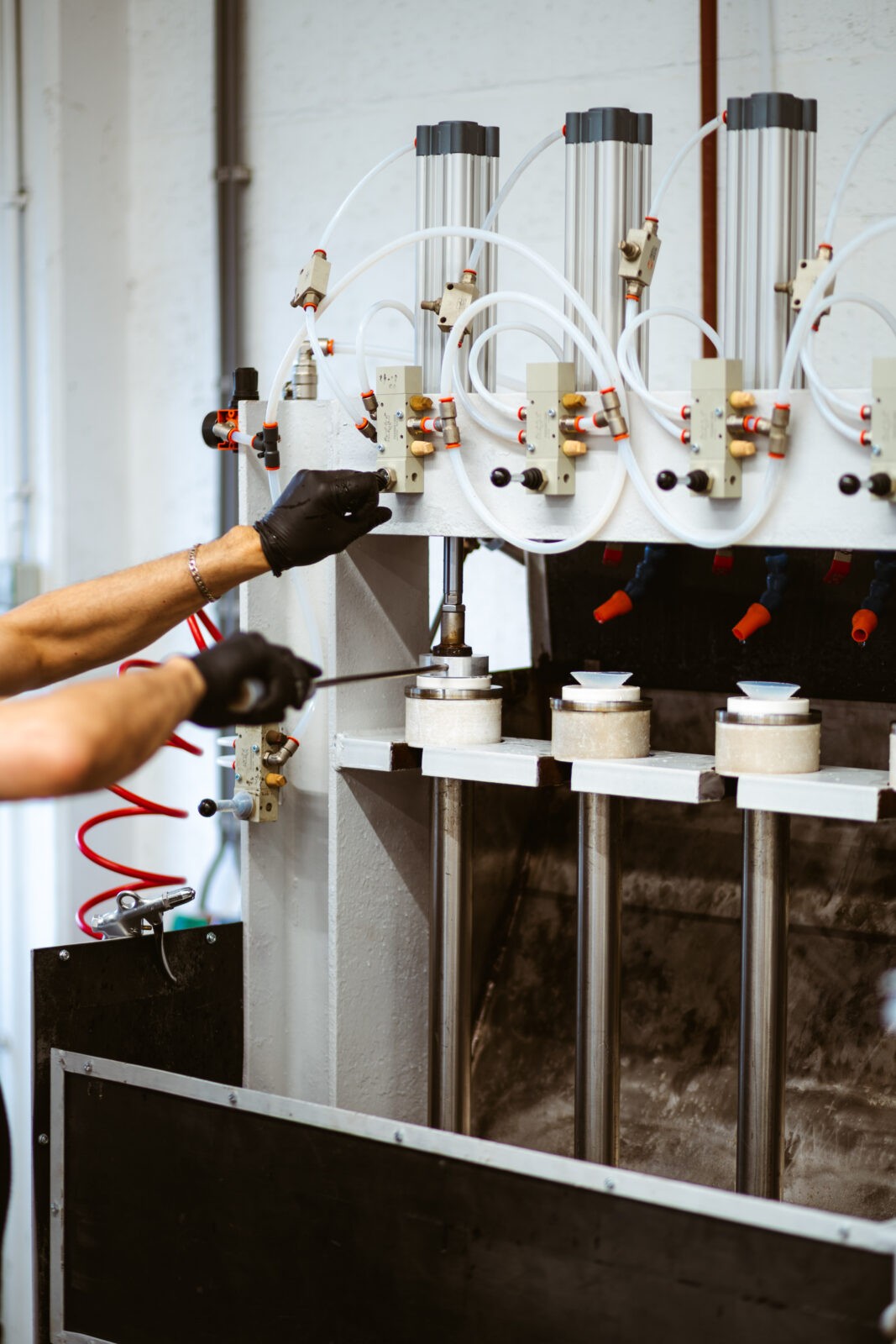
R&D
End products are devised together with the customer in order to offer an ideal PTFE solution.
In-House Engineering
Full engineering of assembly machines is carried out by our subsidiary Soeterbroek Engineering so that customer demand can be optimally fullfilled.
Quality
All products are checked according to customer specifications by our quality department.